What Are 3 Trends & Challenges Facing Downstream Markets?
Despite uncertainty and vulnerabilities around everything from the supply chain to climate change, the global petrochemical market is still expected to see a compound annual growth rate (CAGR) of 4.9% between now and 2026.
Downstream end-use products include plastics, packing, medical equipment, detergents, tires, fertilizers, pharmaceuticals, automotive, and construction. With lingering inflation, some predict downstream will continue to be challenging throughout 2023.
In fact, the International Monetary Fund predicted a gloomy and uncertain outlook for 2023. Nonetheless, demand for end-use products will put pressure on downstream companies to increase production capacity.
When you dig into what is occurring downstream today – the buzzwords often include circularity, transformation, decarbonization, sustainability, supply chains, and resilience.
There’s a lot to unpack under each of these terms. But to dig into the big picture, we turned to a report by Reuters, North American Downstream Trends Report.
They point to emerging trends and challenges surrounding capital projects (CapEx); reliability and maintenance; and shutdowns and turnarounds. Let’s take a closer look at these three areas:
1. CapEx Projects Poised to Boom
Many factors have combined to cause delays in downstream capital expenditures (CapEx) projects. These include a combination of global events, project delays, labor shortages, and reduced CapEx availability, according to Reuters.
However, by 2025, the total global energy sector CapEx is projected to increase by 18% compared to the 2016-to-2020 period, according to S&P Global.
While much of the growth will be in transmission and distribution spending ($433 billion), renewables ($367 billion), and oil and gas ($209 billion), they see global downstream CapEx to grow in the second half of the decade.
Meanwhile, McKinsey is pointing to a general boom in capital projects.
McKinsey believes the world will see “a once-in-a-lifetime wave of capital spending on physical assets between now and 2027. This investment surge —amounting to roughly $130 trillion—will flood into projects to decarbonize and renew critical infrastructure.”
What are some of the potential headwinds?
A significant downstream CapEx project risk stems from on-site problems, such as labor shortages that can lead to delays and cost overruns.
One way to reduce these risks is to complete as much of the project as possible offsite. For example, constructing prefabricated modules offsite.
Reuters cites an ExxonMobil-SABIC joint venture plant in Texas that maintained construction throughout COVID by using offsite-built modules to cut the on-site workforce by half.
No doubt, tech tools—from software platforms to AI—can also play a role in improving CapEx execution. For example, many will use plant camera feeds to spot safety and compliance violations.
AI is used to review video footage and, within seconds, spot violations, such as workers without hard hats and safety gear. By using automatic detection systems, companies can rely on technology instead of manually reviewing video footage.
McKinsey notes how CapEx planning is transformed with advanced analytics. They urge companies to use these tools at every stage—from planning to real-time process tracking. They use the example of an oil and gas company using AI-based analytics to forecast project duration and identify high-risk activity for a project that was delayed more than a year.
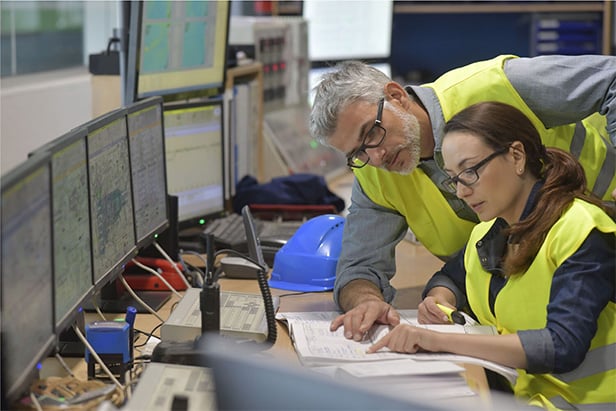
2. Data & Analytics Can Improve Predictive Maintenance
Traditional reactive maintenance, scrambling to fix problems as they occur, is costly and causes delays. Regarding reliability and maintenance, the downstream industry has begun to embrace predictive maintenance technology in a big way.
ResearchAndMarkets notes the market for predictive maintenance technology should reach $18.7 billion by 2027. The market was expected to grow at a CAGR of 26.5% from 2021 to 2027.
Using sensors to continually monitor assets can help to predict a fault long before it happens. This means maintenance crews can complete repairs, upgrades, and replacements during planned service interruptions.
In fact, predictive maintenance systems can detect 90% of faults up to five months before failure with a 200% typical ROI for the equipment, according to the failure detection technology provider Samotics.
There is growing interest in adopting such systems downstream as part of wider moves to use technology for improved maintenance and reliability. “One of the things that we’re trying to do better is to use technology right to improve our processes,” said Jimmy Jernigan, assistant director of global maintenance and reliability at LyondellBasell, during a Downstream USA 2022 panel discussion.
During COVID, it became clear how maintenance strategies impacted resilience.
At the time, there was a concern about maintaining operations with reduced workforces and restrictive working conditions. Today, this has grown to include cybersecurity worries.
For example, the 2021 ransomware attack on Colonial Pipeline highlighted the danger of the industrial infrastructure being targeted by cybercriminals. The incident impacted consumers and airlines along the U.S. East Coast.
While digitization can help make downstream companies more resilient, technology can also address new requirements around transparency and accountability.
This means technology is not just improving how fast work can get done, but also ensuring accuracy. Workers can digitally capture data with handheld devices, sensors, cameras, and drones. But this real-time data must be optimized so it can have an impact on improving operations and maintenance strategies.
3. Minimizing Delays in Shutdowns & Turnarounds
Downstream shutdown and turnaround activities have been hampered by many challenges in recent years—from acquiring materials like gaskets and control valves to a tight skilled labor market. Post-COVID concerns and the war in Ukraine only complicated things.
With over 50% of turnarounds going over budget, procurement departments have had to get creative—from safeguarding supplies to searching for alternative vendors.
McKinsey points out how problematic the skilled labor market is today. They note that 41 percent of the current U.S. construction workforce is expected to retire by 2031, and construction wage trends far exceed recent rates.
Many downstream players use change programs to improve project planning and minimize delays and cost overruns. With stronger owner-supplier relationships, they are more capable of delivering against expectations.
When it comes to turnaround decision-making, more businesses are turning to digital tools to help with scope determination, intervals and timing, product demand and supply, storage and inventory buildups, blocked-out months, spending profiles, and budgets, according to Reuters.
Data can also help deliver safer, more efficient, and more cost-effective turnarounds.
When combined with external contractors on-site, the sheer number of tasks happening during a turnaround can dramatically increase the safety risk. When companies can harness real-time data, information, and analytics, they can improve their decision-making and deliver higher productivity.
For example, former maintenance manager Bruce Grissom said he took a 31% productivity rate and improved it to about 50% using a contractor spend management software, TRACK. One of the biggest benefits to using a digital solution was that he could identify skill levels every day and knowing “when the skill level 1 versus the skill level 4 ratio began to get out of proportion.”
If turnarounds aren’t just routine periodic maintenance events but increasingly large, complex projects, they must meet a broader range of objectives. These can include everything from providing a predictable cost and schedule performance to meeting regulatory targets to maintaining safety.
Take the Next Step with Digitization
Many of these downstream trends and challenges will ultimately be solved using data and advanced analytics—especially when leveraging operational and safety-related data.
It appears downstream operators are becoming more comfortable with the benefits digitization can deliver—especially around operational and safety-related data.
By transitioning from traditional methods to digital solutions, Natalia Klafke, head of Radix Engineering and Software’s North American energy business, notes that some players have begun fusing digital and engineering knowledge for everything from feedstock supply decisions to creating a virtual control tower equipped with AI.
Data underpins all these considerations—how to address everything from adapting existing processes to ensuring staff is properly trained to support digital initiatives.
For example, digital technology can play a major role during the busy turnaround season—especially when it comes down to automating contract compliance. Many downstream players discover a contractor spend management solution can prevent leakage.
Take the next step. Find now how TRACK can help produce error-free invoices and calculate accurate hours and costs for all contractor labor, equipment, and materials.